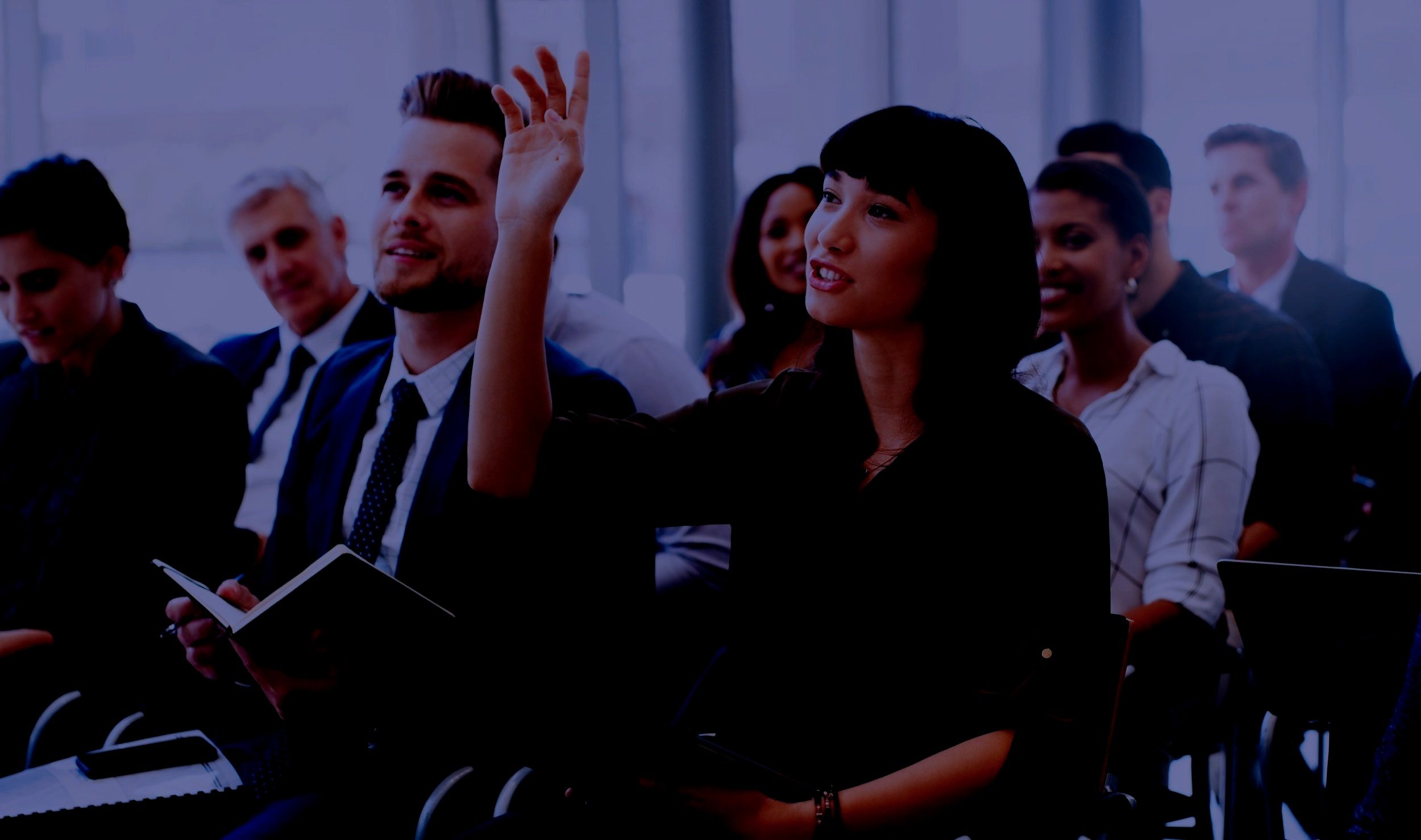
What the experts say about energy performance …
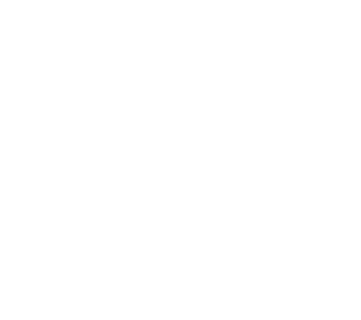
International Energy Agency
Introduction
In late 2020 Carbon IntelliSense was created when we started to notice, just as the IEA noted in 2021, a tightening of energy markets and a focus on controlling carbon emissions.
We understood that there was a need for both the supply of clean energy sources and importantly for us the need for the use of modern IoT technologies, to provide, using Data Forensics, Insight into energy usage, to protect consumers, to mitigate some of the upward pressure on energy prices and climate policies.
In October 2022, the IEA estimated that 75M people globally, would not be able to afford to keep the power on by the end of 2022*
*IEA October 2022 Outlook
Global Pandemic / Ukraine Invasion
The IEA has noted that energy markets began to tighten in 2021 ,because of a variety of factors, including the exponential rapid economic rebound following the pandemic. This situation escalated into a global energy crisis following Russia’s invasion of Ukraine in February 2022.
In the United Kingdom, the Environmental Act 2021 requires that at least one target is set in each of four priority areas, air, water, biodiversity, resource efficiency and waste reduction.
A Public Consultation was published in May 2022 and these targets are to be laid as draft to Government by 31 October 2022 and will come into force once approved by Parliament.
Recession
Slowed economic growth is pointing towards some countries heading towards severe recession. Europe, whose gas supply is uniquely vulnerable because of its historic reliance on Russia, could face gas rationing this winter, while many emerging economies are seeing sharply higher energy import bills and fuel shortages.
While, at the same time, there is ever increasing pressure to implement controlled carbon emission policies
High Inflation / Closures
While Europe, works out how to remove the need to rely on Russian Gas, which is not a short term, we face natural gas , electricity and oil price record highs.
Higher energy prices will and are contributing to painfully high inflation.
Some factories and organisations will need to cutback on output or even shut down, if the use of energy and the associated carbon emissions are not controlled and optimised.
Our market agnostic platform as a service and integrated NON INTRUSIVE IoT hardware, provides the ability to FORENSICALLY identify where and why your energy is being used in real-time.
Our platform will provide insight into how to optimise your energy usage and reduce carbon emissions, as a by-product.
Manufacturing Slowing
The IEA have stated that some gas-intensive manufacturing plants in Europe have slowed output because they can’t afford to keep operating.
Factories in China, have in certain situations, simply had their power supply cut.
We suspect that this will not be the end of power cuts, globally
Climate Policies
Climate policies have been blamed in some quarters for contributing to the recent increases in energy prices.
Research carried out by the IEA confirmed that there was no evidence, to validate this statement.
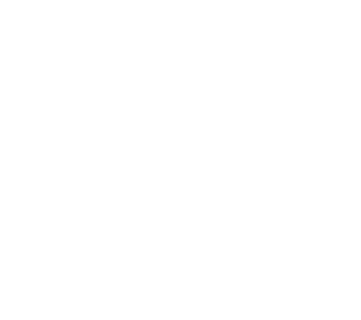
World Economics Forum
Global Economic Leaders
The World Economic Forum is the International Organization for Public-Private Cooperation. The Forum engages the foremost political, lobal business, cultural and other leaders of society to shape global, regional and industry agendas.
Increases in inflation and exponential increases in energy costs together with increases in Carbon Emissions associated with generation of electricity, the correct operation of, and the potential mis-performance of your assets means that you need to take action, which is endorsed by the World Economic Forum.
Please take a look at their statistics, which we detail here.
Tackling the current energy crisis
82%
Measures to reduce energy consumption
64%
Diversification of energy sources
59%
Direct cash transfer to households and businesses
Achieve energy security
100%
Improving energy efficiency
90%
Diversifying sources of energy imports
86%
Reducing energy consumption
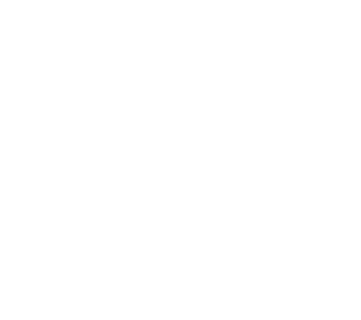
Deloittes
Introduction
Maintenance and reliability professionals in the manufacturing industry face a number of challenges, but the goal of any maintenance organisation is always the same: to maximize asset availability.
Poor maintenance strategies can reduce your overall productive capacity by 5 to 20 percent.
Recent studies show that unplanned downtime is costing industrial manufacturers an estimated $50 Billion each year.
This begs the question, “How often should a machine be taken offline to be serviced?”
Traditionally, this dilemma forced most maintenance organisations into a trade-off situation, where they had to choose between maximizing the useful life of a part, at the risk of machine downtime (run-to-failure), or attempting to maximize uptime through early replacement of potentially good parts (time-based preventive maintenance), which has been demonstrated to be ineffective for most equipment components.
Maximum utilisation of tooling or machine components can be achieved by running them until they fail. But this can lead to catastrophic machine damage as parts begin to vibrate, overheat, and break, reinforcing the old adage “pay me now or pay me later.”
And, while run-to-failure may be an acceptable approach for some assets, it still needs to be understood that unplanned downtime is almost always more expensive and time consuming to correct.
Conversely, you might consider more frequent replacement of parts and servicing of equipment. But this can not only increase replacement costs over time, it can also increase planned downtime and disruption to operations.
Spare-parts management presents a similar challenge that can feel like a constant balancing act. With limited budgets, maintenance professionals must evaluate which parts they’ll need and when to procure them.
If the spare is not on hand or on order when it’s needed, the downtime of an asset can be anywhere from days to weeks—or even months—while waiting for the replacement part. This typically leads to the build-up of spares inventory, which not only ties up working capital, but also increases the risk of excess and obsolescence that erodes the bottom line.
Internet of Things
The Internet of Things (IoT) is perhaps the biggest piece of the Predictive Maintenance and equipment being operated outside of best practice, puzzle.
The internet as we know it connects your laptop and mobile devices to data streamed and stored continuously in the cloud from your assets.
IoT translates physical actions from machines from sensors such as temperature, vibration, or conductivity.
Once the physical actions have been streamed and translated, they are processed, aggregated, analysed and converted into actionable insight, associated with your entire production network.
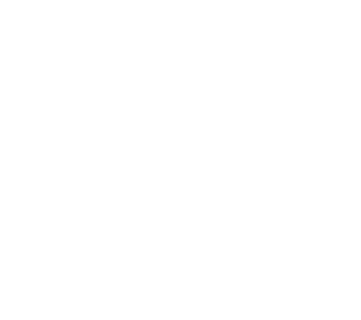
Toyota Manufacturing
Challenge
Toyota Manufacturing want to reduce the utilities cost required to produce a vehicle by 7.5%, year on year.
Toyota identified which equipment consumes most energy at transformer level, but they needed be able to see consumption and the performance of equipment at a granular level to establish whether equipment was performing optimally, in real-time.
Solution
Toyota installed 300 wireless current monitoring sensors to energy-intensive key significant equipment, to monitor energy consumption and machine condition.
Toyota created an energy map of their production process.
Toyota installed pulse counters to understand gas consumption, as well as CO2, temperature, and humidity sensors to monitor status on the shop floor and keep optimal indoor air quality conditions for team members through HVAC systems.
Benefits
Monitoring energy-intensive key significant equipment energy consumption and machine condition to identify energy patterns and anomalies.
One injector used for service parts was identified as using excessive energy, another about to fail. The injectors were modified or replaced respectively, to perform within acceptable parameters, in order to prevent manufacturing shutdown.
Savings on this piece of equipment alone has realised energy consumption in non-production periods reduce by 82%.
Mitsubishi Technology
Challenge
Creation of an end-to-end energy management solution to accurately measure energy consumption at a machine level, without stopping production.
Solution
Installation of non-evasive plug-and-play energy monitoring sensors.
Benefits
Continuous real-time energy monitoring has facilitated energy reduction processes, such as machines left running and outdated machines causing suboptimal performance and abnormality identification, in advance of unplanned downtime, reducing energy consumption by 10%.
RS Components
Challenge
RS Components, with operations in 32 countries, is the world’s largest distributor of electronic, electrical, and industrial components.
RS wanted to monitor the performance of two of the most critical elements of their conveyor systems, lowerator and elevator, which pass packaging totes between floors during the order fulfilment process, to predict costly breakdowns, estimated to by Deloitte to run at 42%. In their UK distribution centre alone, over 2,000 motors are used to power over 7km of conveyor systems.
Solution
They main three indicators that a motor is running smoothly are vibration, temperature and current. Any changes to normal operating conditions can indicate a fault or potential breakdown, so by monitoring the electrical current, temperature and vibration, the facilities team would have an insight into the health of each conveyor.
Sensors were fitted to each conveyor to monitor the condition of each asset.
Benefits
Equipment performance data is transmitted in real time and displayed in a dashboard in the facilities control room, with any performance anomalies triggering indicators.
RS Components, with far greater awareness of how well motors are performing can plan maintenance, when convenient.
Predicative main maintenance increased equipment uptime and availability by 10% to 20% and reduced overall maintenance costs by 5% to 10%.
Cavendish Engineering
Challenge
Cavendish Engineering were commissioned by their client British Land, to improve the efficiency of workspaces across their London portfolio, initially at a 12-storey office block in Paddington, London.
An audit revealed the ventilation system was highly inefficient. It was running at full speed, throughout the working day, with energy being used to supply fresh air regardless of need.
Solution
Cavendish Engineering retrofitted CO2 sensors on each floor of the building to obtain accurate measurements of CO2 levels throughout the day, in order to control the air handling units based on demand.
The sensors used, use wireless technology, and are solar-powered, making them easy to install and incredibly low maintenance. They offer a high level of accuracy (within 125ppm) while remaining cost effective.
Benefits
Rather than running at full speed all day, units respond to increases in CO2 levels as occupancy increases. As well as preventing the building from wasting large amounts of energy, the technology also gives facility management teams full, 24/7 visibility of workspace conditions.
The project has delivered a 42% reduction in air handling, a 15% reduction in gas consumption and a 10% reduction in electricity consumption since its completion.
BI Norwegian Business School
Challenge
BI Norwegian Business School is the largest business school in Norway and the second largest in Europe, with four campuses, with its main one located in Oslo.
With over 10,000 students and staff living on the campus, the school wanted clearer insights into how its space was being used so managers could make more data-driven, fact-based decisions.
The challenge was to keep track of how its various zones were being used. The school wanted to have clear visibility of utilisation of different areas, such as workspaces, canteens and reading rooms.
Solution
The first step was to carry out a pilot project to record and report on the way these zones were being used and at what times and to use the idea harvested to develop innovative solutions and services to offer added value for everyone.
The school developed a platform that ingests data from sensors around the campus, which is then interpreted to analyse noise, temperature, air quality, movement patterns, needs-based cleaning or occupancy in areas at different times.
Benefits
The data insights from the pilot project have informed the development of processes and systems to manage regional campuses in Bergen, Stavanger and Trondheim.
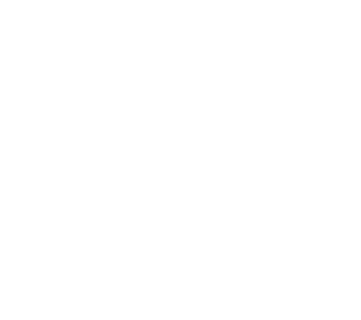
News & Media
What would two degrees of global warming look like?
Sir David Attenborough's address to World Leaders at COP26
What would three degrees of global warming look like?
World Energy Outlook 2022 and the transition to clean energy
Do something about your Carbon Emissions today
Transporting goods around the world
What is a Digital Twin and how does it work?
What is Logistics IoT